What is Metrology?
Metrology is the science of measurement and can sometimes be overlooked despite being an essential aspect of manufacturing. To ensure that all component parts fit together and work properly, it is essential to perform this inspection.
As a manufacturer, you will want to consider not just the cost of a project, but the accuracy, reliability and speed of production. It is important to consider where in this process it is best to carry out the measurement. This will vary depending on your industry.
Types of Inspection
Volume production will rely on a sampling inspection strategy. Automotive component producers can be used to measure a small number of parts from each batch to ensure consistency throughout production.
However, any application which relies on safety will usually need 100% inspection. This would include aerospace manufacturers as accuracy and safety are paramount for a long-standing good record.
Industry 4.0 brings forth the rise of smart manufacturing technologies which, in themselves, add new and diverse complexities within the inspection process. Smart factories that are being developed will find these manufacturing technologies integral to their success. The aim is to develop more efficient manufacturing that allows for products to be customised. Thereby boosting manufacturing around the world.
A study carried out by Accenture predicts that Industry 4.0 could add as much as $14.2 trillion to the global economy by 2030 and that this will be driven by smart factory solutions.
Smart Factories and Industry 4.0 Challenges
Industries are moving towards hyper-personalised experiences, products and services. Innovative business models will result in new sources of revenue.
Smart factory metrology has an important purpose, giving greater visibility of the entire supply chain which includes the suppliers. The process will be smarter, faster and easier to action using smart metrology equipment within the future factory. The factory equipped with industrial robots and automated material handling relies on automated control systems built on timely verifications and feedback.
To make industry 4.0 a reality, it is clear that organisations need to work together. Industry 4.0 solutions rely heavily on connectivity, both technically and organisationally. Inter-connectedness requires better data flow and more visibility, which means it is essential to have interoperability.
Manufacturers need to adapt their inspection processes, overcoming physical barriers and closing the gaps in metrology information at each stage of the value chain in order to support digital, autonomous production.
Factors to Consider When Adapting Metrology to the Needs of the Factory
Inline Metrology
Inline metrology, measurements carried out as part of the process, has many advantages over traditional methods for manufacturing operations. Rather than having inspection as a separate activity, that can cause delays through having to move the parts to the inspection department; Inline inspection will speed up the process by allowing some of the process steps to be removed.
By measuring parts in-process, it is possible to reduce rework and scrap by detecting problems earlier and preventing those problems from going unnoticed causing more delays. The inline inspection provides the opportunity to correct a problem while the part is on the machine, which will minimise the impact of any rework needed.
In-process measurement can help detect problems before they occur. An early detection of any variation may make it possible to take corrective action before a problem occurs by compensating for the variation.
Non-Contact: Optical and Laser Systems
Non-contact metrology, which includes laser scanners, phase-based laser scanning and optical systems, are crucial to smart factories. This type of measurement allows for high-resolution scanning of parts as well as long-distance manoeuvring of measuring devices.
The challenges with non-contact metrology are that this method typically has line-of-sight limitations. It requires highly accurate positioning to measure the detailed features such as holes. The Metrology Hub at the University of Huddersfield is working to increase the technology’s capability for high dynamic range measurement. The aim is to improve the ability of metrology to measure pieces more effectively from a distance while maintaining extremely high levels of accuracy.
Robots
Introducing robots into a factory has proven to increase accuracy, reliability and continuous production. Robots are not usually designed to measure parts. However, it is possible to adapt them for inspection. This would be useful for larger volume components.
The optimal robotic inspection is the 100-micron tolerance area and above. Typically this is the level at which the beneficial flexibility and speed of a robotic system outweighs its inherent accuracy limitations as opposed to a dedicated measuring device.
Each generation of Robotics is continually getting smarter and improving accuracy, demonstrating that machine-based measurement and inspection will only increase.
The Rise of Smarter Inspection Tools
The Industry 4.0 revolution is seeing the science of inspection rapidly evolve.
An EU-funded and multi-partner project, SYMPLEXITY, has been launched to research and improve how humans and robots collaborate. Specifically in the application of industrial polishing. Currently, at least 90% of finishing work is carried out by hand, according to the consortium. However, it is believed that robots could reduce this manual polishing to a level of around 20%. With the rest being carried out by robots under human supervision.
It is notoriously difficult to evaluate polished surfaces and even highly skilled humans will need to make subjective judgments on whether the finished part is good enough. The SIR Cell uses a surface finish sensor to measure the surface quality and can report on as many as 13 data parameters.
Symplexity is developing the strategy to see surface quality data using augmented reality, AR. AR could present the information directly on to the surface negating the need for flat 2D on-screen representations that require you trying to visualise how a parameter change could affect a part.
What this means in practicality is that some of the subjectivity can be removed. Enabling users to make informed decisions more quickly. Human experts will still approve the results for the foreseeable future, but when measurements of properties are so quantifiable, the data can be connected directly to the quality assessment process.
Keeping Up With the Competition
Metrology is going beyond research, with suppliers developing technologies that have better measurement capabilities. Manufacturers will need to embrace these new methods to stay vital in their industry and not lose out to competitors.
Improved measurement will support the evolution of connected factories. It will help reduce downtime and speed up production while producing better designed and higher quality products. Now really is the time to start updating the inspection process and take advantage of the smarter and more affordable measuring tools that are emerging.
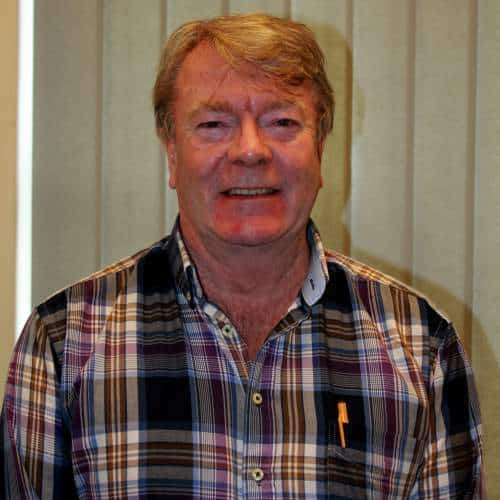
Jeff Eley is the founder and managing director of Eley Metrology, a leading company in the precision measurement industry. With decades of experience in metrology, Jeff has established himself as a respected figure in the field. Under his leadership, Eley Metrology has become renowned for its expertise in coordinate measuring machines (CMMs), digital height gauges, and granite metrology products. Jeff’s vision has driven the company to develop innovative solutions, including custom-designed CMMs and the flagship long-bore measurement machine (LBM). His commitment to excellence and customer-centric approach has positioned Eley Metrology as a trusted provider of high-precision measurement tools and services for industries such as aerospace, automotive, and manufacturing.