In many manufacturing plants, you can’t move for waste. Manufacturing defects waste materials, products waste time sitting in storage, and managers waste time on churning employees. However, with lean manufacturing, you can turn this waste into an opportunity for improvement. But what is lean manufacturing? Well, learning more about the history, principles, and legacy of lean manufacturing helps you unlock its benefits and revolutionise your firm.
What is Lean Manufacturing in Industrial Production?
Lean manufacturing, as the name suggests, prioritises sleek and efficient production with no room for indulgence or misdirected resources. Simply put, this discipline minimises waste while maximising value. Using precision techniques and precision measurement equipment, lean manufacturing seeks to eliminate waste of all shapes and sizes. Everything that doesn’t contribute value becomes an error under lean.
Crucially, the method also takes a customer-centric approach to working out what is and isn’t valuable. If customers want to pay for it, it’s valuable; if they don’t, lean manufacturing streamlines it for the better.
Japanese Roots
Industry leaders trace lean’s origins to the dialogue between Eastern and Western manufacturing research, specifically between the US, the UK, and Japan in the 20th century. One foundational text, Frederick Winslow Taylor’s The Principles of Scientific Management (1911), turned the management of production lines into a science to be measured and improved upon. Taylor’s stated that, in manufacturing, ‘wherever the new method is found to be markedly superior to the old, it should be adopted as standard’.
But what is lean manufacturing in a Japanese context? Well, Toyota employees Taiichi Ohno and Shigeo Shingo applied Winslow’s teachings to their company in Tokyo, laying the foundations for lean manufacturing worldwide. The pair devised an effective system for manufacturing Toyota vehicles, known as the Toyota Production System (TPS). When Shingo published The Toyota Production System: Beyond Large-Scale Production in 1988, it set the stage for lean manufacturing worldwide.
What is Lean Manufacturing in 7 Types of Waste
Shingo’s work outlines seven categories of industrial waste, helping businesses manage their inefficiencies and strive for success. Shingo categorises waste by Transportation, Inventory, Motion, Waiting, Overproduction, Overprocessing, and Defects. These seven categories evolved into eight in the dialogue between theory and practice in the East and the West. Businesses added an 8th type of waste, skills, to the existing seven. Some use the acronym TIMWOODS to remember these types, and help measure them in their workplaces.
Transportation Waste
Getting your supplies from A to B, and your products from B to C creates all kinds of waste. From the distances to the routes and the vehicles themselves, reducing transportation waste helps you save resources and accelerate your manufacturing.
Inventory Waste
Businesses often stock warehouses high with mouldering products, and empty warehouses rack up expensive building costs on electricity and air-con. The moment a product expires, gets dropped, or gets stolen from your inventory, there’s valuable waste to be managed.
Motion Waste
Transportation waste also occurs on a far smaller scale. Rather than transporting goods to and from your production line, motion waste includes the motion of your workers and equipment within the plant. Small changes to each motion, whether tightening a bolt or moving a workpiece to and from a machine, make huge differences over time.
Waiting Waste
Production and supply lines often face long delays. When manufacturers wait for materials and customers wait for products, money goes to waste.
Overproduction Waste
Exceeding your customer’s demand for a product strains your inventory waste, and can also devalue your product as scarcity disappears. What is lean manufacturing’s solution to overproduction waste? Just in time, or JIT, production tactics which supply goods just in time for demand to arise.
Overprocessing Waste
Any processes that don’t add value to your product waste time and money. If part of your manufacturing line fails to add quality, quantity, safety, or demand, it creates waste.
Defect Waste
Defects encompass one of the most frustrating elements of manufacturing waste when your production line fails at the final hurdle. Defects occur when manufacturing plants deliver ineffective or sub-standard products. If you catch them before they reach customers, they reveal wasted resources. However, defective products in the hands of customers spell expensive product recalls, reimbursements, and loss of priceless reputation and satisfaction.
Skill Waste
Finally, wasted skills occur when companies fail to employ the right people in the right roles. Dynamic businesses upskill and promote their employees, adding value to their workforce and boosting their morale. By contrast, wasteful companies stagnate, with over-skilled employees burning out of their plants.
Lean manufacturing and its History in the West?
Business leaders in Europe and North America saw Toyota categorising and eliminating waste through each of these categories, and developed the concept of lean manufacturing. But what is lean manufacturing’s most seminal text? Lean thinking: Banish Waste and Create Wealth in your Corporation, written by James Womack and Daniel T. Jones in 1996. Jones and Womack drew five principles from the Toyota Production System, outlining the core tenets of modern lean manufacturing.
What is Lean Manufacturing in Five Simple Principles
Customer Value
Jones and Womack state that lean manufacturers put themselves in their customer’s shoes and see which elements of their products deliver the most value.
Value Stream
Lean manufacturers then follow this value up through the production line, seeing which elements of manufacturing create value and which create waste.
Creating a Smooth Flow
With value now mapped to your production processes, lean manufacturing suggests you streamline each step of the way, creating a smooth and seamless transition across the manufacturing line.
Pulling, Rather Than Pushing, Demand
This principle refers to the JIT production strategy, where manufacturers predict demand and create products just in time to meet it.
Kaizen
Drawing directly from a Toyota term, Womack and Jones also highlight Kaizen, the concept of continuous improvement. Persisting over time, lean manufacturers optimise each stage of production, seeing success as a journey rather than a destination.
Conclusions: What is Lean Manufacturing
Lean manufacturing involves categorising, identifying, mapping, and eliminating waste. Effective measurement supports effective management, and when you measure your waste, lean manufacturing helps you manage to streamline it for success.
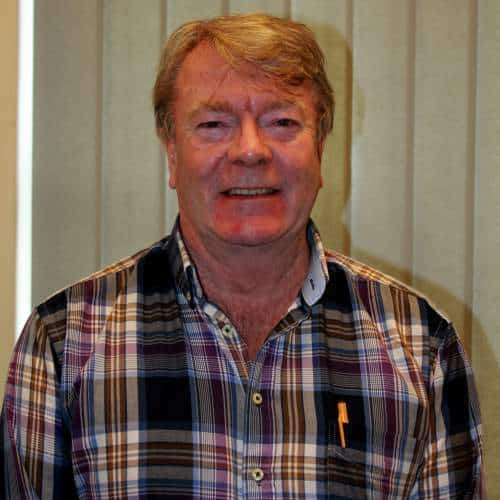
Jeff Eley is the founder and managing director of Eley Metrology, a leading company in the precision measurement industry. With decades of experience in metrology, Jeff has established himself as a respected figure in the field. Under his leadership, Eley Metrology has become renowned for its expertise in coordinate measuring machines (CMMs), digital height gauges, and granite metrology products. Jeff’s vision has driven the company to develop innovative solutions, including custom-designed CMMs and the flagship long-bore measurement machine (LBM). His commitment to excellence and customer-centric approach has positioned Eley Metrology as a trusted provider of high-precision measurement tools and services for industries such as aerospace, automotive, and manufacturing.