Quality is synonymous with successful businesses. However, nobody’s perfect. We’ve all felt that disappointment when your plans don’t quite pan out, or your prized new product meets some serious hitches. Fortunately, industries offer solutions to these issues, so you can try, try, and try again until your processes improve. We call these solutions quality assurance and quality control, under the quality management umbrella. Defining quality assurance vs quality control and applying techniques from each discipline into your workflow helps you and your business improve. Each error quashed and each improvement incorporated creates a more efficient, successful, and high-quality business for your team and your customers to enjoy.
What is Quality Assurance?
Quality assurance involves improving your processes to minimise the risks of errors in your workflows. It’s a management strategy from the top down. Quality assurance professionals essentially take data about existing errors in the end product and develop strategies to mitigate them earlier in the process. Incorporating this data with tried and tested theory, expertise, and strategies, they improve quality bit by bit. Crucially, they use an iterative approach, applying small tweaks here and there. When these tweaks pay off, they maintain and increase them. When these tweaks lead to errors and unsatisfactory products, they’re caught by quality control teams.
What is Quality Control?
Quality control, by contrast, involves inspection, correction, and communication around product errors. It’s often the last line of defence between customers and a bad customer experience. In that sense, it’s vitally important for maintaining brand image, customer retention, and product quality. Quality control teams help detect faults and inconsistencies, nipping them in the bud before they get any worse. They also inform decisions about whether to scrap and recall faulty products, or offer short-term workarounds and fixes while the quality assurance team change their strategy. The handover point between these teams helps us understand the main differences between quality assurance vs quality control.
Quality Assurance vs Quality Control – Understanding the Differences
It’s actually quite hard to identify the differences between quality assurance and quality control – after all, they’re both different types of quality management. However, the devil’s in the details; when you break things down by categories, it’s far easier to differentiate their valuable nuances.
Timelines
We already know that quality control focuses on the end product. Quality assurance, on the other hand, looks at the process as a whole, right from the beginning of pre-production.
In terms of their timescales, quality assurance presents a long-term approach. Meanwhile, quality control delivers short-term fixes on a JIT (Just in Time) basis.
The two disciplines also differ in their historical timeline. Businesses popularised quality control in the 1920s and 30s, far before the rise of quality assurance. Quality control blossomed with the introduction of Fordist production lines, where mass manufacturing highlighted the need for quality checks at the end of the line.
The proactive approach to improving processes as a conscious departmental objective didn’t hit the mainstream until decades later. Scientists in Japan and the US added statistical analysis techniques that would later be known as quality assurance throughout the 1950s and 60s.
Objectives
The overarching objective remains the same in quality assurance and quality control, high-quality products. However, the specific objectives inherent in their strategies highlight the differences within.
Quality control experts take samples to verify standards. Quality assurance experts measure efficiency in teams and machinery to plan improvements. Quality control takes a reactive approach to discovering and correcting errors, while quality assurance takes a proactive approach to improving systems and preventing errors.
When it comes down to it, both disciplines share an objective, but differ in their methods of achieving that objective.
Methods
These two disciplines take different approaches to supporting product quality, and their differing approaches require manifestly different methods. Typically, quality control deploys practical methods, while quality assurance prioritises strategic methods.
Quality Control Methods
Quality control’s main method, inspection, faces a decisive obstacle: inspecting every dimension of every product consumes lots of time. If you inspect every inch of every product, you may still face human error, and the time it takes would impede efficiency and distribution.
Quality control teams manage the sample sizes they inspect, varying the sample sizes to find the right balance. This technique works best when it measures up to the company’s standards, keeps the customers happy, and provides enough data for their quality assurance team.
Quality Assurance Methods
Planning often dominates the first stages of any quality assurance approach. Armed with the insights they learn from the quality control teams, quality assurance professionals plan their solutions, apply them at small scales, check the results, and then decide whether to roll them out across the business. Working in tandem, both quality assurance and quality control create well-run, successful companies.
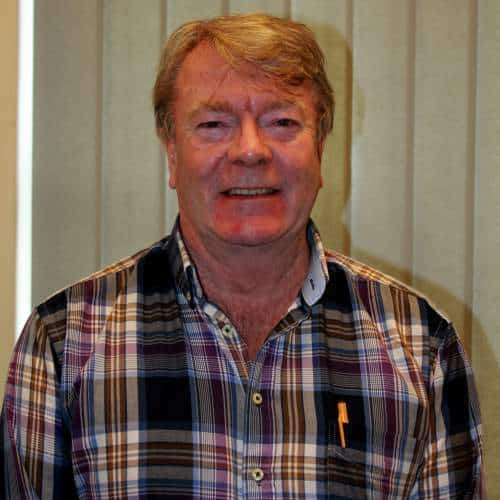
Jeff Eley is the founder and managing director of Eley Metrology, a leading company in the precision measurement industry. With decades of experience in metrology, Jeff has established himself as a respected figure in the field. Under his leadership, Eley Metrology has become renowned for its expertise in coordinate measuring machines (CMMs), digital height gauges, and granite metrology products. Jeff’s vision has driven the company to develop innovative solutions, including custom-designed CMMs and the flagship long-bore measurement machine (LBM). His commitment to excellence and customer-centric approach has positioned Eley Metrology as a trusted provider of high-precision measurement tools and services for industries such as aerospace, automotive, and manufacturing.