Precision engineering requires tight tolerance and high-quality machining, and that’s where metrology comes in. Metrology, or the science of measurement, develops advanced automated machines and AI modelling to analyse workpieces and maintain production, but it also improves the basics to perfection. Engineers use straightforward, effective, wireless tools like gauges to perform all manner of quality control. Learning about the different types of gauges in metrology helps you understand their wide-ranging uses and benefits.
What Are Gauges in Metrology?
Metrologists design gauges to determine the minimum and maximum acceptable tolerances of a given dimension. Engineers then use these gauges to assess whether workpieces meet these tolerances. They ask the simple ‘yes’ or ‘no’ question of acceptability to support practical quality control. Gauges in metrology provide a vital line of defence against inconsistency. This front-line tool for engineers and manufacturers stands as a pillar of production excellence.
Ten Different Types of Gauges in Metrology
Gauges in metrology come in all shapes and sizes, with designs matching any and every workplace dimension. Here’s a list of ten common designs and their purposes in the industry.
Ring Gauges
The ring gauge supports quality control in workshops with cylindrical equipment or products. It also features no electronics and no moving parts. As the name suggests, ring gauges use a ring-shaped or toroidal structure to measure the external diameter of cylindrical workpieces. Workshops simply invest in ring gauges with internal diameters that match their desired specifications, enabling efficient measurement and quality control.
Snap Gauges
Similar to ring gauges, snap gauges also measure diameters. However, their shape delivers different applications. Snap gauges use a ‘C’ or ‘U’ shaped frame to measure diameter, with a gap between their measurement section for inserting and moving a workpiece. This enables them to measure specific features on larger equipment or measure diameters of products in frames or other bulky structures that couldn’t be measured by a ring gauge.
Calliper Gauges
One of the most common types of gauge in metrology, you may recognise the calliper gauge from school. Featuring a measurement shaft with two jaws at one end, the calliper gauge adjusts its jaws to measure the diameters within. Different designs use dials, digital displays, or mechanical units to determine the given diameter.
Wire Gauges
Wire gauges resemble a circular saw blade, except with holes of increasing diameters where a saw blade’s teeth would be. Users compare these holes with wires they wish to measure, determining the diameter relative to whichever hole it fits in. This supports precise measurements for electrical wiring or the strings of musical instruments.
Height Gauges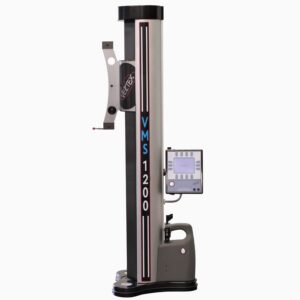
A straightforward and reliable tool, a basic manual height gauge features a baseplate, a perpendicular column, and a measuring arm attached to a slider. Users adjust the arm via the slider to determine the height of a given product relative to the baseplate. More advanced digital height gauges are also available, which offer a big step up in accuracy as well as a host of additional features.
Plug Gauges
Another example of straightforward and practical gauges in metrology, plug gauges come in handy for measuring internal holes and cavities. Resembling a dumbbell, plug gauges feature a central shaft with large heads on either end. The central shaft features go/no go readings to indicate the minimum and maximum depths, akin to readings on a car’s fluid reservoirs. Users simply insert a plug gauge and measure the depth against the readings.
Feeler Gauges or Thickness Gauges
Feeler gauges resemble a folding fan, featuring metal measurement blades attached at one end by a hinge pin. Engineers use these gauges to measure the gaps between two components in a given product. By finding the corresponding number of feeler gauge blades to measure a given gap, you can effectively measure your products against their minimum and maximum tolerances. The tolerances on gaps in equipment prove vitally important in any industry, as contact between moving parts can cause dangerous malfunctions.
Radius Gauges
Radius gauges use a similar fan of measurement blades to feeler gauges, except they’re designed to measure curves and radii in concave and convex shapes. Blades designed to measure convex shapes feature dimples of different sizes, which users compare with their product to find the most similar shape. For concave shapes, the radius gauge features blades with convex protrusions, measuring radii in an inverse fashion.
Screw Pitch Gauges
Screw pitch gauges support quality control for screws and other helically threaded equipment. These gauges resemble feeler gauges, yet they feature two sets of fanned measuring tools, with one pinned at each end of a central shaft. Each measuring blade in each fan features teeth which mirror the crests and roots of a screw, so you can compare each one to a given screw to measure its pitch.
Dial Gauges
Dial gauges use two main components to measure evenness on a surface plane: a dial and a probe. Simply run the probe over a surface plate or other important plane, and the dial moves when the probe detects cracks, bumps, pressure changes, or other inconsistencies.
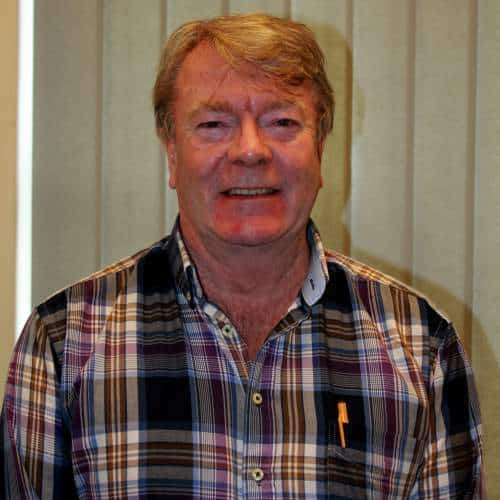
Jeff Eley is the founder and managing director of Eley Metrology, a leading company in the precision measurement industry. With decades of experience in metrology, Jeff has established himself as a respected figure in the field. Under his leadership, Eley Metrology has become renowned for its expertise in coordinate measuring machines (CMMs), digital height gauges, and granite metrology products. Jeff’s vision has driven the company to develop innovative solutions, including custom-designed CMMs and the flagship long-bore measurement machine (LBM). His commitment to excellence and customer-centric approach has positioned Eley Metrology as a trusted provider of high-precision measurement tools and services for industries such as aerospace, automotive, and manufacturing.