Humanity owes a lot to granite. As a natural substance, it’s rich with important properties for engineering and construction. Granite was formed millions of years before humans (or any mammals) even existed, so it had plenty of time to wait before it started occupying our kitchens and workshops. However, it now forms an important pillar of our industrial engineering, as well as literal pillars in ancient and modern buildings alike.
From the crust on our earth’s surface to the granite surface plates in our workshops and laboratories, its importance is undeniable. Understanding more about granite’s history, and its properties, clarifies this importance, helping us understand why precision engineering needs granite and why it’s here to stay.
Granite’s Material History
Our history with granite dates back beyond the written word. Scientists in Sweden found Bronze age paintings adorning vast granite shelves, named the Namforsen rock art. The art depicts boats, animals, and hunting parties, drawing upon granite’s sturdy and durable qualities to leave a lasting message about ancient culture.
We get the word ‘granite’ from the Romans, who named the rock granum after its grained patterns. While noticing its aesthetic qualities, the Romans also made the most of granite’s physical properties. They used granite blocks for paving and architecture, building famous roads, aqueducts, and pillars in temples and bathhouses from granite. The fact that these monuments outlived the Roman empire by almost 2000 years reveals granite’s enduring fortitude and the wisdom of Roman engineers and architects in selecting them for their projects.
The Different Types of Granite
Italian granite still proves popular to this day, topping kitchen counters around the world. However, you can also find and quarry the stone in the UK, from sites in Devon and Cornwall. Granite makes up around three-quarters of the earth’s crust, so you can find it on pretty much any landmass around the world. It’s primarily made of quartz and feldspar, but other minerals included in its composition create a range of shades and colourations, from pinks and reds to greys and blacks.
What Makes Granite so Useful for Precision Engineering?
Granite sticks around in workshops to this day for some good reasons. With modern engineering capabilities and requirements to the thousandth of a millimetre, granite offers a unique combination of trustworthy qualities that make it the bedrock of precision engineering.
It’s Non-Metallic and Rust-Proof
Engineers used cast iron for workshop baseplates and measuring equipment during the industrial revolution. Granite made a commercial appearance at the turn of the 20th century before the world wars, and grew in popularity as metal became scarce.
As an alternative to metal, granite also offers a rust-proof and unreactive surface. By eliminating cast iron plates, and the rust flakes they entail, engineers unlock clean and reliable workshop measurements.
It Has Low Thermal Expansion
Granite resists the expansion and warping that other materials face under extreme heat. Engineers measure this property as a thermal expansion coefficient, and granite’s coefficient of 8 is far lower than iron’s, at 12. This low coefficient creates a stable material for precision engineering. Granite’s heat resistance suits it to the workshop, the fireplace mantle, and the crust above the earth’s mantle alike.
It’s Flat and Non-Porous
Granite creates a far less porous surface than sedimentary stones like limestone or sandstone. Its closed-pore composition allows the surface to resist impurities from spillages and other contaminants. This quality decreases the risks of stains, swelling, and cracks.
It’s Dense and Durable
Our planet formed granite in a slow process deep below the earth’s surface, creating a dense, thermally homogenous material built to last. The lack of internal inconsistency, and lack of internal tensions, results in a durable stone, suiting the predictability required for precision engineering.
Granite’s Modern Uses
We’ve already discussed granite’s utility in ancient societies. However, the stone finds plenty of uses in modern homes and workplaces, beyond the statues, temples, and canvasses of old. The chances are, you’ve seen granite adorning a home, either in a kitchen or bathroom. The same durability and non-porousness that draws engineers towards granite makes the stone ideal for bathroom tiles or kitchen backsplashes.
These qualities prove essential for professional modern workshops and laboratories. Beams, measurement triangles, rails, and granite surface plates all use the stone to keep their action precise and reliable.
How To Use a Granite Surface Plate
Granite surface plates make the most of the stone’s durability and reliability to support a range of precision engineering goals. Crucially, they provide a stable horizontal plane for measurement. From there, engineers carry out design, repair, assembly, gauging, marking, toolmaking, and quality control on their workpieces of choice.
We’ve established granite’s durability, but it’s not invincible. Granite surface plates require maintenance and cleaning themselves, including calibration and resurfacing from time to time. That being said, they’re one of the most important tools in an engineer’s arsenal.
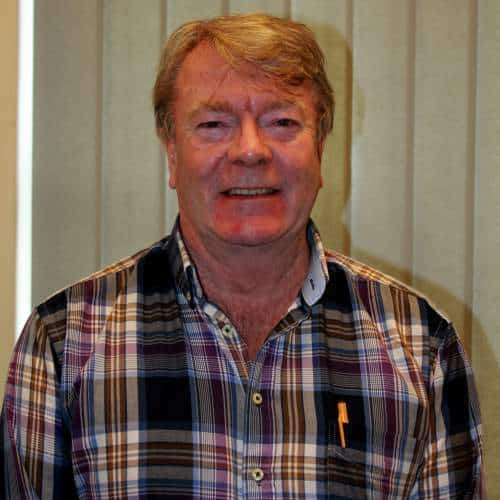
Jeff Eley is the founder and managing director of Eley Metrology, a leading company in the precision measurement industry. With decades of experience in metrology, Jeff has established himself as a respected figure in the field. Under his leadership, Eley Metrology has become renowned for its expertise in coordinate measuring machines (CMMs), digital height gauges, and granite metrology products. Jeff’s vision has driven the company to develop innovative solutions, including custom-designed CMMs and the flagship long-bore measurement machine (LBM). His commitment to excellence and customer-centric approach has positioned Eley Metrology as a trusted provider of high-precision measurement tools and services for industries such as aerospace, automotive, and manufacturing.