The foundation of precision measurement is the surface plate. Granite surface plates are considered the more superior material compared to cast iron surfaces. The properties of Granite such as weight resistance and durability, create a super smooth surface that is easy to maintain. Granite surface plate maintenance may be easy, but it is still important to perform regular checks and cleaning.
The Importance of Accurate Measurement
As engineering and manufacturing specifications require ever tighter management, the importance of accurate measurement is crucial. From the local machine shop to aerospace manufacturers, precise measurement is pivotal. Each type of Metrology equipment requires a base plate to measure from. A Granite surface table would be used as a base for a digital height gauge and larger machines, such as a Bridge CMM, have a granite surface plate as part of the machine.
Granite Surface Plate Maintenance
Your granite surface plate is one of your most important parts of equipment. Due to its flat surface, it can be often be mistaken for a table. However, it is certainly not designed as a place to pop down your coffee cup! When not in use your table should be protected by a cover. To help ensure your surface plate is well cared for here are five expert tips for granite surface plate maintenance.
1. Regular Service and Calibration
• Regular granite surface place calibration ensures optimum accuracy
• Regular calibration will identify if resurfacing is required. Calibration will check the surface for any dents or marks missed by the naked eye. If a plate requires resurfacing, Eley Metrology can work on-site or remove the plate to so the work can be carried out in our laboratory
• With constant use, calibration intervals can vary from 6 months to 1 year. With infrequent use, calibrations can be up to 3 years or longer. Check your quality manual regarding the interval of calibration set by your company
2. Keep it Clean
• The measurements done on the surface plate have very fine margins and any dirt, dust or grease could affect the results. A dirty surface plate will also wear away more quickly
• Get into the habit of using professional granite cleaning fluid before and after use
• Have two cloths set aside to keep for surface plate cleaning. Use the first soft cloth to wet the entire surface with cleaning fluid. Use a second dry soft cloth to dry in circular motions. Any solution left in the granite micropores will quickly evaporate and the surface will be ready to use. Make sure you clean the cloths regularly
• To protect the surface from dust building up use a cover when not in use
3. Plate Rotation
• Rotate the plates from time to time as this reduces localised wear spots forming
• If you have large plates to rotate and use machinery to lift them, it is best to use nylon straps for lifting. Avoid any contact with metal lifting equipment which could scratch the surface
• When measuring small parts use different points on the surface plate, so wear and tear is not in the same place every time
4. Surface Plates are not Storage Benches
• Using your surface plate to store tools or foods can speed up surface wear and cause damage to the granite. Use surface plates for intended use only
• When the surface plate is not in use place a protective cover over it
5. Avoid Overload
• Overloading can cause accuracy issues and may even cause serious damage. Ensure even distribution is applied over the surface if possible
• It is important to make sure you have the right size surface plate for the equipment or tooling you need to measure. If you are unsure what size is correct contact Eley Metrology for help
How to Care for Your Granite Surface Plates
Following our five expert tips will certainly ensure the longevity of your surface equipment, but wear and tear is unavoidable. To protect your measuring surface, it is important to perform regular service checks and calibration for optimum and precise results.
The Eley Metrology Granite Range
At Eley, our granite metrology standards range has incorporated the expertise of the Crown Windley name to ensure the highest quality products for our customers. Our granite surface plates are hand-lapped by our highly skilled precision engineers in accordance with the specified standards. We also recondition granite surface plates back to their original specification.
Service contracts are available on granite artefacts, and our engineers can visit on-site to minimise downtime for your company. Alternatively, your granite equipment can be sent to our Derby headquarters to be resurfaced and calibrated in our temperature-controlled laboratory.
Granite Surface Plates are available in a wide range of sizes. At Eley Metrology we specialise in the manufacture of bespoke granite products. If you have a specialist requirement, please get in touch with our team.
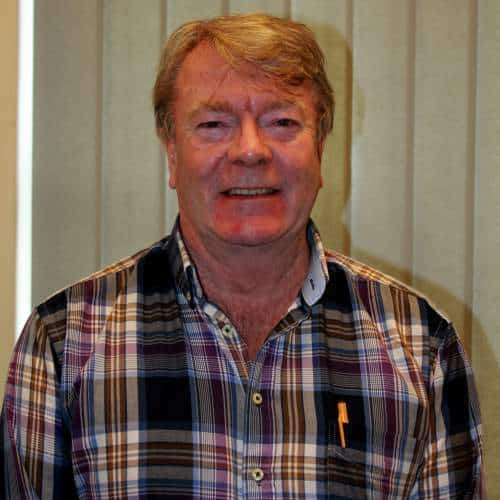
Jeff Eley is the founder and managing director of Eley Metrology, a leading company in the precision measurement industry. With decades of experience in metrology, Jeff has established himself as a respected figure in the field. Under his leadership, Eley Metrology has become renowned for its expertise in coordinate measuring machines (CMMs), digital height gauges, and granite metrology products. Jeff’s vision has driven the company to develop innovative solutions, including custom-designed CMMs and the flagship long-bore measurement machine (LBM). His commitment to excellence and customer-centric approach has positioned Eley Metrology as a trusted provider of high-precision measurement tools and services for industries such as aerospace, automotive, and manufacturing.