As metrology evolves, it is becoming increasingly intelligent and automated with improved accuracy and precision. As digital transformation accelerates, the tools commonly used, such as coordinate measuring machines (CMMs) and height gauges, are being augmented by smart sensors, AI and automated data feedback loops.
When combined with human expertise, we arrive at metrology 4.0.
Metrology 4.0: Measurement in the Digital Age
Metrology 4.0 is a term that reflects the integration of digital technologies, Internet of Things (IoT) devices, and data analytics into traditional measurement processes. It enables real-time decision-making, better traceability and more intelligent quality control.
For example, under 4.0, CMMs will communicate directly with production machinery, enabling closed-loop manufacturing. They may influence the components checked, automatically adjusting machining parameters on-the-fly if tolerances are not met.
They also build on existing capabilities to create inspection paths in complex processes. This convergence of measurement and manufacturing reduces errors, waste and costly downtime.
Evolving Tools: Smart, Connected and Fast
Today’s metrology tools are not going to disappear. For example, height gauges, CMMs and even granite surface plates will remain foundational but will be enhanced by new capabilities.
Smart height gauges with digital readouts, wireless data transfer and integration with SPC (Statistical Process Control) software will no longer be passive. Instead, they will actively feed into a larger quality ecosystem where real-time decisions, notifications and simulations are run.
Consider granite surface plates, used to provide a stable base for precision measurement equipment . They will often be equipped with environmental sensors to monitor temperature and humidity. When paired with calibration services, they help ensure long-term accuracy in highly controlled environments.
Coordinate Measuring Machines (CMMs) will be increasingly equipped with multi-sensor heads (optical, tactile and laser), and AI-assisted software that simplifies programming, speeds up inspection and reduces operator expertise. They will also integrate with other systems to provide streamlined, end-to-end processes.
However, the future of metrology can also connect services outside of an organisation, integrating the entire supply chain. As parts need to be replaced or impromptu maintenance is required, orders can be made intelligently without involving a human.
These upgrades increase measurement throughput while reducing human error, leading to greater productivity and less waste during production, and more accuracy during research and development.
The Role of Artificial Intelligence and Automation
AI is perhaps the most transformative aspect in the future of metrology, yielding a predictive and adaptive function, not just a control mechanism.
AI-based algorithms will analyse measurement trends to identify tool wear or part deformation before it causes a failure. Early automatic or manual intervention can then occur.
Machine learning models can suggest optimal inspection plans based on historical part data, and automated CMM programming can reduce the need for specialist input, allowing general technicians to handle more complex inspections with ease.
The ability to predict when a part in machinery needs to be replaced becomes a more accurate process that minimises downtime.
Digital twins will play a significant role in the future, offering accurate simulations and modelling that can enable predictive maintenance, optimised operations and faster design iterations.
Quality Across the Product Lifecycle
Although traditional metrology was primarily focused on final inspections, it is now utilised throughout the product lifecycle, from design and prototyping to production and final inspection. This trend is expected to continue into the future, with a greater emphasis on automation and intelligent decision-making.
For example, digital metrology platforms will work directly with CAD models, enabling virtual inspection plans and simulation-based tolerancing. Real-time data from shop-floor devices, such as smart probes on machine tools and intelligent sensors, can be fed back into design loops, driving continuous improvement.
This integrated approach is particularly effective when supported by robust tools, such as calibrated height gauges and granite plates, which serve as physical references for verifying sensor accuracy and surface flatness during inline processes.
Human Expertise Will be Essential
While automation and AI are revolutionising workflows, human expertise remains essential. For instance, humans will be needed for:
- Interpreting complex or ambiguous data, particularly where there are edge cases
- Designing effective measurement strategies
- Managing uncertainty and ensuring traceability
- Validating AI outputs and calibrating sensitive instruments
As calibration services evolve, they will also provide consulting and training to help teams apply best practices, which is essential for leveraging advanced technologies securely, effectively and ethically.
Value-added services will include digital calibration certificates and verification, automated scheduling reminders, and even remote diagnostics to streamline the service process.
Calibration, Traceability & Compliance
Precision depends on trust, and that trust is built through calibration and traceability. Future-ready metrology providers will be incorporating:
- Calibration compliance services
- Cloud-based asset management systems for instrument tracking
- Predictive calibration intervals based on usage analytics
These practices reduce downtime, ensure compliance and help businesses stay audit-ready. This is essential in safety-critical industries, such as aeronautics and medicine, where calibration and traceability are regulatory requirements. Accurate measurements begin with certified tools, which offer reliability throughout the production process.
Overcoming Challenges and Realising the Benefits
Despite the opportunities, companies face challenges in adopting Metrology 4.0:
- There is a high cost of new CMMs and automated systems
- A need for retraining staff in digital tools
- Integration with legacy systems and ERP platforms
However, the cost-benefit analysis should yield a positive rate of return, offering faster inspections, improved quality, reduced waste, and stronger competitiveness. Metrology partners who sell tools such as CMMs and height gauges, and also provide calibration, training, and digital integration support, can facilitate this transition.
Embrace the Intelligent Future
The future of metrology is intelligent, connected and collaborative. By combining advanced tools like smart CMMs, metrology and manufacturing system integrations with wireless tools, AI, and human expertise, manufacturers can achieve a new level of precision and agility.
Whilst these tools and systems will take time to evolve, keeping up to date with technical advancements will enable businesses to adopt a metrology strategy for the future. Real-time decision-making, analytics, and futuristic models, such as the digital twin, will transform manufacturing towards lights-out. Whether this materialises into reduced prices remains to be seen.
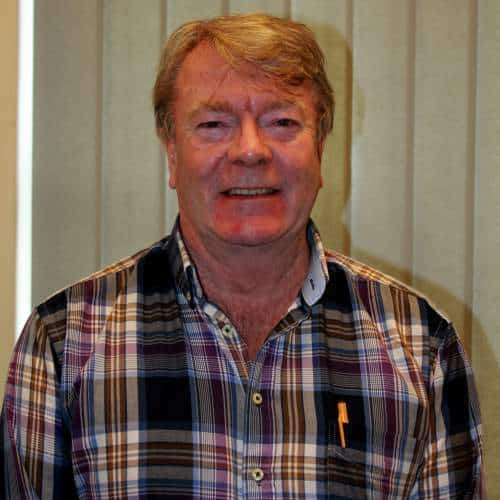
Jeff Eley is the founder and managing director of Eley Metrology, a leading company in the precision measurement industry. With decades of experience in metrology, Jeff has established himself as a respected figure in the field. Under his leadership, Eley Metrology has become renowned for its expertise in coordinate measuring machines (CMMs), digital height gauges, and granite metrology products. Jeff’s vision has driven the company to develop innovative solutions, including custom-designed CMMs and the flagship long-bore measurement machine (LBM). His commitment to excellence and customer-centric approach has positioned Eley Metrology as a trusted provider of high-precision measurement tools and services for industries such as aerospace, automotive, and manufacturing.