In any scientific or technical field, accuracy and precision are critical aspects of measurement. However, various factors can affect both, leading to errors or variability in results.
Understanding what influences accuracy and precision, such as instrument quality, environmental conditions, human error, and calibration, can help minimise measurement discrepancies and improve the reliability of your results.
This article will address the key factors that affect measurement accuracy and precision and how to effectively reduce unreliable results to improve the quality and consistency of the collected results.
The Difference Between Measurement Accuracy and Precision
Measurement accuracy refers to how close a measured value is to the actual or accepted value. It indicates the correctness of a measurement.
Precision, on the other hand, describes the consistency or repeatability of measurements, meaning how close the measurements are to each other, regardless of whether they are accurate. Both accuracy and precision are essential in scientific and technical measurements.
What can Impact Measurement Accuracy and Precision?
Several factors can affect measurement accuracy and precision—below is a list of ways in which they can be impacted and tips for improving measurement results:
Environmental Conditions
Environmental factors such as temperature and humidity can dramatically influence measurement accuracy and precision, especially when dealing with sensitive materials like metal that can expand and contract with temperature changes.
Your measuring environment must be temperature-controlled to ensure consistent measurement accuracy and precision. Maintain a consistent temperature to mitigate material expansion and keep humidity low. Excess moisture can cause metal measuring tools to rust, affecting their reliability.
Surface Conditions
Dirt, dust, or debris on a surface where an object is being measured can lead to inaccurate results, especially when measuring flat objects or using precision tools like callipers or micrometres, which rely on direct, consistent contact for accuracy.
Small gaps may not be visible to the naked eye but can still affect the accuracy of the measurement by preventing complete contact between the object and the measured surface. Therefore, the surface, object and measuring tools must be all thoroughly cleaned before taking a reading.
Additionally, consider using a flat, smooth, rigid graded surface plate, such as those made from granite, certified for precision measurement to provide a stable reference plane. Surface plate calibration will ensure a truly flat surface within a known tolerance, and the certification will ensure traceability.
This increases the potential that any measurement tool or workpiece deviations will be accurately detected and corrected. These granite plates’ inherent resistance to thermal expansion and mechanical wear further enhances their reliability in maintaining precision over extended periods of use, making them an essential tool in high-accuracy environments.
Operator Skills and Consistency
Human errors compromise measurement accuracy and precision even when precise instruments and the environment are controlled. An inexperienced or fatigued operator may apply inconsistent pressure on instruments, misread scales, or improperly align measuring devices.
It’s advised that all operators be well-trained in using specific measuring tools and consistent in their methods. Establishing standardised measuring procedures in your workplace is vital to avoid variations in readings caused by differences in personal techniques.
Another option would be to use digital measurement devices, which is a more effective way to reduce the chances of misreading or misinterpretation.
Calibration and Maintenance of Instruments
Even the most advanced tools can lose their accuracy over time due to wear and tear, environmental changes or improper usage.
If you suspect measurements shift over several weeks or months, you should consider recalibrating equipment even if it is scheduled in the future.
To ensure you are keeping track of when calibrations are due, consider keeping a maintenance log for each instrument. Routine maintenance can also help to extend your tool’s lifespan by spotting potential issues early.
Material Surfaces and Finishes
Rough surfaces or inconsistencies on tools, such as burrs and scratches, can introduce errors by warping the contact points of the measuring instrument.
Inspecting the surface finish of your tools before measuring is crucial for accuracy and precision. For delicate measurements, consider using non-contact measurement methods like a laser, which can reduce the impact of surface imperfections.
Flooring and Structural Vibrations
Flooring and overall structural stability of the room, machinery, foot traffic or nearby construction where measurements are taken can cause tiny shifts in sensitive instruments, affecting results.
You should set up precision measuring equipment on stable surfaces in areas free from excessive vibrations.
If this is not feasible, consider using vibration-damping systems or isolation pads under the measuring tools and machines. In high-precision environments, ensure the floors are level and made from materials that reduce vibration transmission.
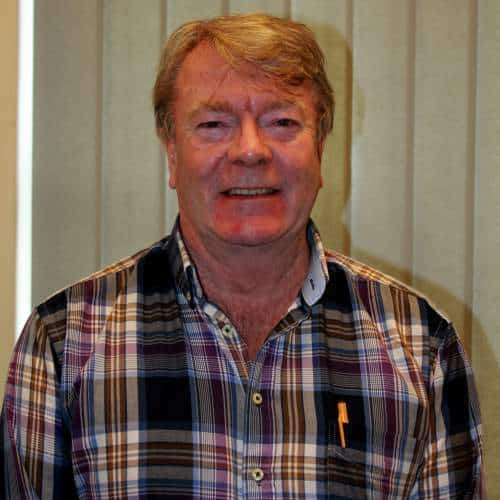
Jeff Eley is the founder and managing director of Eley Metrology, a leading company in the precision measurement industry. With decades of experience in metrology, Jeff has established himself as a respected figure in the field. Under his leadership, Eley Metrology has become renowned for its expertise in coordinate measuring machines (CMMs), digital height gauges, and granite metrology products. Jeff’s vision has driven the company to develop innovative solutions, including custom-designed CMMs and the flagship long-bore measurement machine (LBM). His commitment to excellence and customer-centric approach has positioned Eley Metrology as a trusted provider of high-precision measurement tools and services for industries such as aerospace, automotive, and manufacturing.