Industrial automation in metrology, the science of measurement, revolutionised how manufacturers ensure quality and accuracy in their processes. By integrating advanced automation technologies, businesses can achieve higher levels of precision, reduce human error and enhance productivity.
This article explores the benefits of industrial automation in metrology. We highlight its role in driving innovation, improving quality control and optimising operational efficiency in various industries.
Enhanced Precision and Accuracy
Precision and accuracy are paramount in industries like aerospace, automotive and medical devices, where even minor errors can lead to significant consequences. Automated systems excel in eliminating the variability associated with human error, consistently performing measurements with a high degree of repeatability. For example, automated coordinate measuring machines (CMMs) can measure complex geometries with micron-level accuracy, significantly surpassing the capabilities of manual measurement.
Efficiency and Productivity Gains
Automated measurement systems can operate continuously, unlike human operators, who require breaks and are prone to fatigue-induced errors. This capability enables 24/7 operation, leading to a higher production rate and faster turnaround times. Moreover, automated metrology systems can inspect parts in line, immediately identifying and addressing defects before they progress further in the production process. This real-time quality control reduces waste and ensures that only parts meeting stringent quality standards move forward.
Data Availability
Automated systems can efficiently collect, store, and analyse vast amounts of measurement data. This data can be used for statistical process control (SPC), helping identify trends, detect anomalies, and make informed decisions to improve processes, sometimes in real time. Advanced software tools can integrate with automated metrology systems, enabling manufacturers to maintain rigorous quality control standards and traceability over time. Further, collecting historical data can lead to continuous improvement, driving a more innovative and competitive business.
Versatility and Adaptability
Automated systems versatility allows manufacturing companies to streamline their operations, reduce labour costs and improve productivity by leveraging automation systems for different functions within the same workflow. As automated systems are incredibly adaptable, they can quickly respond to a changing production requirement and be reprogrammed with minimal downtime if and when the market demands shift or new products are introduced.
Scalability and Flexibility
An automated system’s scalability ensures business can expand their operations to accommodate product demand without additional investment. Automated systems are flexible in that they can be reprogrammed and reconfigured to respond to a swift shift in marketing demands or the introduction of new technology without significant disruption. This enhances a business’s capability to innovate and stay ahead of competitors. These are essential ingredients for maintaining competitiveness and achieving sustainable growth.
Faster Inspection Process
Automated systems significantly increase efficiency and speed up inspection processes. They reduce the time required to assess products, leading to faster throughput and shorter production cycles. As previously mentioned, this efficiency is complemented by improved accuracy, as automation reduces human error, resulting in more consistent and precise inspections. Within the manufacturing industry, the combination of speed and precision translates to a win for productivity.
Cost Savings
Automation increases the throughput rate and increases quality control through advanced notification. There is enhanced profitability with more units produced per unit of time and early warning of defect production. Automated systems also require less human intervention, reducing labour expenses and minimising the risk of costly workplace accidents. Over time, the investment in automation pays off through decreased maintenance costs and extended equipment lifespan, ultimately providing a substantial return on capital investment and contributing to overall cost efficiency.
Health and Safety Benefits
Automated systems with precision measurement equipment can conduct precise measurements in high-risk areas, significantly reducing workers’ exposure to hazardous conditions and lowering the chances of accidents and injuries. These systems operate with unparalleled accuracy and reliability, leading to fewer measurement errors and minimising the need for rework, which can be time-consuming and costly.
Additionally, these industrial automation systems take over repetitive and strenuous manual tasks, which are often the root cause of chronic musculoskeletal disorders among workers. This reduced risk profile could also contribute to savings in liability insurance. Overall, automated systems promote a healthier working environment for employees in the long term.
Embracing the Future of Precision and Efficiency
As technology continues to evolve, the integration of automated metrology systems will become even more seamless and impactful. By embracing advancements in automation and real-time data processing, manufacturers can stay ahead of the competition, ensure higher quality standards and pave the way for a future where precision and efficiency go hand in hand. Investing in industrial automation in metrology is not just an option but a necessity for forward-thinking businesses aiming to thrive in the modern industrial era, delivering products of excellent quality and striking a great relationship with their customers.
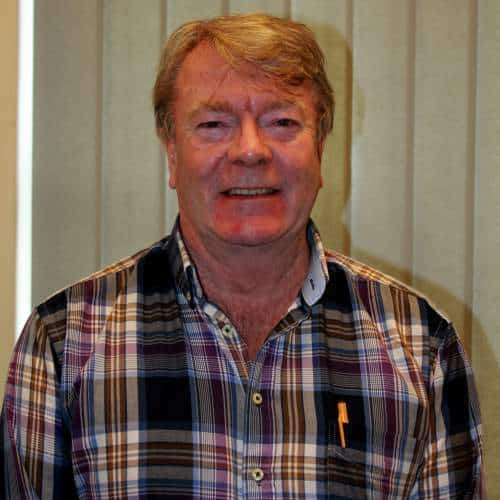
Jeff Eley is the founder and managing director of Eley Metrology, a leading company in the precision measurement industry. With decades of experience in metrology, Jeff has established himself as a respected figure in the field. Under his leadership, Eley Metrology has become renowned for its expertise in coordinate measuring machines (CMMs), digital height gauges, and granite metrology products. Jeff’s vision has driven the company to develop innovative solutions, including custom-designed CMMs and the flagship long-bore measurement machine (LBM). His commitment to excellence and customer-centric approach has positioned Eley Metrology as a trusted provider of high-precision measurement tools and services for industries such as aerospace, automotive, and manufacturing.