Poka-Yoke is a methodology used in the manufacturing industry to enhance quality control by preventing errors before they occur. This proactive approach is deeply embedded in the lean manufacturing philosophy and focuses on designing processes that inherently reduce the chances of mistakes.
This article will explore Poka-Yoke in manufacturing and its various applications across different sectors, highlighting its effectiveness.
What is Poka-Yoke?
Poka-Yoke, a Japanese concept for “error proofing,” Was formalised by the visionary Shigeo Shingo in the 1960s. His innovative approach aimed to design the manufacturing process so that errors are virtually impossible, inspiring a new era of quality control. This concept became a vital element of the Toyota Production System, demonstrating the profound impact of his contributions.
Poka-Yoke’s Success Story With Toyota
Thanks to the pioneering work of Shigeo Shingo, Toyota has effectively implemented error-proofing techniques in its manufacturing process. These include using autonomic control to stop machines automatically when issues are detected, installing sensors and cameras to ensure car parts are correctly placed and standardising work processes to reduce mistakes.
What’s more, Toyota promotes the participation of its employees in quality circles, where they can collaboratively problem-solve Poka-Yoke solutions. This inclusive approach not only prevents errors but also fosters a sense of ownership and pride among the employees.
The success of Toyota’s Poka-Yoke implementation can be seen in its global reputation for minimising waste, improving productivity and maintaining high-quality standards. The effectiveness of Poka-Yoke in Toyota’s operations has influenced other industries to promote and adopt similar error-proofing practices worldwide.
Types of Poka-Yoke Methods
Shigeo Shingo developed three types of Poka-Yoke methods to prevent errors from occurring in mass manufacturing.
Contact Method
The contact method of Poka-Yoke in manufacturing is a crucial quality assurance technique within manufacturing environments, particularly on assembly lines. It primarily focuses on identifying abnormalities in a product’s physical attributes, such as shape, size, colour, weight, or dimensions within the assembly line, by using precision measurement equipment.
Instruments like physical sensors or detectors are employed to scan each product. Any products detected as inconsistent with established standards by these sophisticated tools are alerted to manufacturing personnel or automated systems.
This immediate notification allows for swift corrective actions, ensuring that only products meeting strict quality criteria proceed further in production. This method enhances product reliability and significantly reduces the likelihood of errors propagating through to the final stages of manufacturing.
Fixed-Value Method
The fixed-value method, also known as the constant number method, is a type of Poka-Yoke method that ensures that a precise number of actions occur before a task is considered complete.
It’s beneficial in repetitive tasks, preventing incomplete and redundant actions and guaranteeing that each process cycle is performed correctly and consistently. For instance, a device might count the number of screws needed to secure a cover and alert the operator if any are missing or extra.
Motion-Step Method
This method monitors the steps in an operational sequence to ensure each is completed correctly and within the designated parameters. It is vital for complex processes where the sequence of operations is critical to the product’s quality and functionality.
It provides additional protection against sequence errors and ensures smooth progression through the manufacturing process. Ultimately, it alerts workers when a step has been skipped, allowing them to rectify the error appropriately.
Applications in Manufacturing
Poka-Yoke techniques are applicable in a wide range of sectors. All types of manufacturers are keen to reduce errors and improve safety.
Pharmaceutical
In manufacturing within the pharmaceutical industry, Poka-Yoke ensures the accuracy and safety of medication dispensing. Uniformed colour-coded labels and uniquely shaped pill bottles prevent medication mix-ups, reducing the risk of errors.
Automated dispensing systems also confirm correct dosages with visual and auditory signals, which is crucial in an industry where mistakes can be severe. Additionally, producing child-lock bottles efficiently with Poka-Yoke enhances safety by preventing children from accessing medications that can be life-threatening, increasing overall safety and trust in pharmaceutical products.
Sporting Equipment
Poka-Yoke improves the safety and function of many sports equipment. For instance, weightlifting machines feature automatic locks to secure weights. At the same time, treadmills have a red safety clip that runners attach to themselves to automatically stop the treadmill when pulled if they trip or fall.
Household Appliances
Poka-Yoke features within household appliances can help reduce human error and increase safety. For instance, irons can automatically shut off if they haven’t moved for a while, preventing fires. Similarly, washing machines have sensors that detect overflow or incorrect loading, stopping the machine to prevent water damage and ensure efficient cleaning.
Automotive Safety Features
Poka-Yoke creates safety features to help prevent accidents, ultimately saving lives. For instance, automatic emergency braking systems in newer makes can detect potential collisions and apply the brakes if the driver doesn’t react in time. Additionally, seatbelt reminders alert drivers and passengers to buckle up when the car starts, enhancing overall safety.
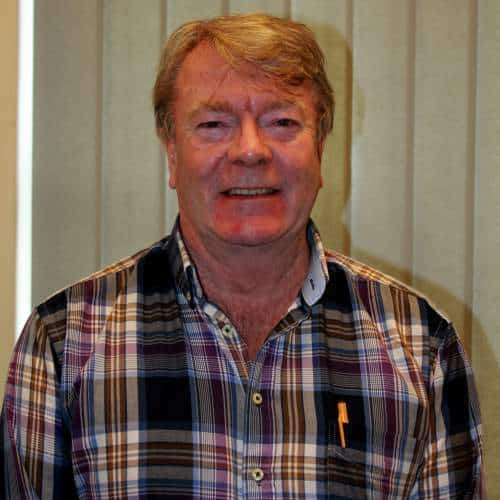
Jeff Eley is the founder and managing director of Eley Metrology, a leading company in the precision measurement industry. With decades of experience in metrology, Jeff has established himself as a respected figure in the field. Under his leadership, Eley Metrology has become renowned for its expertise in coordinate measuring machines (CMMs), digital height gauges, and granite metrology products. Jeff’s vision has driven the company to develop innovative solutions, including custom-designed CMMs and the flagship long-bore measurement machine (LBM). His commitment to excellence and customer-centric approach has positioned Eley Metrology as a trusted provider of high-precision measurement tools and services for industries such as aerospace, automotive, and manufacturing.