Metrology is the science of measurement. Calibration is a practice that ensures the accuracy and precision of the measuring equipment. Those simplified definitions make it easy to understand why calibration in metrology is essential.
Measuring is an integral part of industry: designs, implementation and testing are often completed to specification. They rely upon measuring to ensure quality, safety and efficient production.
This article uses the manufacturing, aerospace and automotive industries to help us understand the importance of calibration in metrology. First, let us look at how metrology and calibration are related.
Metrology and Calibration
Measurements are performed to give us a quantifiable representation of a property such as length, weight or speed. When performing these measurements accurately, it is vital that they can be relied upon. Therefore, they must be precise, providing the same quantity within a specified tolerance for repeated measurements.
Over time, the characteristics of measuring equipment change. Reasons for this include wear and tear, environmental influences and natural degradation due to the materials and components used in the equipment. As a result, the same repeatable measurement can vary over time.
For this reason, many industries rely upon the calibration process to restore the measuring equipment’s accuracy and precision. This could be to ensure production efficiencies or to meet legal or regulatory requirements such as health and safety. Calibration will check the accuracy of the measuring device against known quantities. Any variations will be corrected by adjusting, repairing or replacing the measuring equipment.
Below are examples of why calibration in metrology is important.
Manufacturing
As part of the supply chain, manufacturers have an immense responsibility to ensure that the parts, products and systems they deliver meet the functional and non-functional requirements, such as quality and safety, specified by the customer.
Initiatives such as waste reduction rely heavily upon accurate measurement. When cutting materials or shaping components, any excess material not used leads to wastage. Accuracy also plays a part in the early detection of defects. If a warped component is identified early, it saves production effort and prevents equipment failure.
One measuring device used in manufacturing is the coordinate measuring machine (CMM). They are often used for measuring complex geometries, both online and offline. CMM calibration will ensure the precision of measurement to aid overall consistency in the manufacturing process.
Aerospace
Within the aerospace industry, accuracy is a safety critical feature. At every stage of the production process, strict quality guidelines will specify accurate measurement and tolerance requirements. The reasons for this are obvious: lives depend on it. Failures not only cost substantial sums of money, but they can be catastrophic if they occur mid-air.
Many parts are used throughout production, and accurate measurements must be repeatable. The accuracy of measurement cannot vary. Components must fit together correctly as specified. Therefore, regular calibration of measuring equipment is considered critical.
Whilst we frequently consider commercial planes, the production of vehicles and equipment that enter space is equally important and even more complex. Their components are entering a very different and hostile environment. Measurements will also occur in space as part of monitoring, maintenance and experimentation. We have all seen the catastrophic pictures of component failure onscreen.
Calibration satisfies industry standards for traceability and audit requirements. When it is known that measuring equipment is accurate, the field of error source in measurement is reduced.
Automotive
Accuracy also has a role in the automotive industry. Henry Ford created the moving assembly line, which radically changed vehicle production. As vehicle assembly lines evolved, measuring has become crucial for ensuring smooth production and minimising costs and wastage.
However, it is not only vehicle components that require accurate measurement. Equipment that is used in production also requires accuracy. It may disrupt production or injure a worker if it does not work correctly. Assembly uptime and safety are fundamental metrics in the automotive industry, and measurement accuracy significantly contributes to both.
Like the aerospace industry, non-functional requirements such as safety are critical requirements for vehicles. Not only must an end customer be satisfied and safe, but a wider audience must believe that such a product is of high quality and will meet their expectations should they order the same. Production efficiency depends on volume; the end products drive that volume, so consistency is essential.
Summary of Benefits
As described in this article, accurate measurements support safety and productivity. Efficiency, cost savings and production speed all rely on accurate measurements. This can only be consistently achieved if the equipment making the measurements can provide accurate and precise measurements.
The process by which equipment is checked, adjusted, repaired or replaced to restore accuracy is called calibration, and it underpins the reputation of these industries.
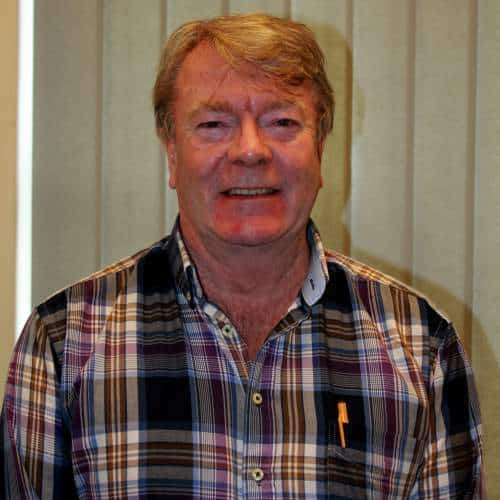
Jeff Eley is the founder and managing director of Eley Metrology, a leading company in the precision measurement industry. With decades of experience in metrology, Jeff has established himself as a respected figure in the field. Under his leadership, Eley Metrology has become renowned for its expertise in coordinate measuring machines (CMMs), digital height gauges, and granite metrology products. Jeff’s vision has driven the company to develop innovative solutions, including custom-designed CMMs and the flagship long-bore measurement machine (LBM). His commitment to excellence and customer-centric approach has positioned Eley Metrology as a trusted provider of high-precision measurement tools and services for industries such as aerospace, automotive, and manufacturing.