Metrology plays a vital role in the automotive industry to help ensure the success of products delivered to the marketplace. From design and prototyping to production and quality assurance, metrology facilitates conformity to design specifications and production efficiencies – whose absence would spell disaster for any automotive business as an ongoing concern.
The automotive industry has made significant strides in recent years due to technical advancements. As such, competition and safety requirements mean that the industry needs to continuously seek improved tools to aid its success through science and engineering. The metrology industry is a crucial provider of such tools.
Below, we explore how metrology offers the automotive industry performance gains fundamental to its success.
Metrology in the Automotive Industry
Ever since the days of Henry Ford, the automotive industry has been pivotal in advancing manufacturing technologies. Metrology has grown with it to provide the accurate and precise measuring capabilities needed to engineer and produce vehicles.
The automotive industry fundamentally relies upon accurately producing and fitting components to provide a vehicle that can offer safety and value for money. It is a dynamic industry, which changes year on year, and the how and when of measuring is critical to the efficiencies and effectiveness of design and production.
At the design and prototyping stage, measurements aid in exploring how a particular engineering idea or concept may work. For example, this could be a manual measurement using a height gauge or an automated measurement using a coordinate measuring machine (CMM). At the production stage, the measurements ensure that components’ geometries are within specified tolerances to achieve quality assurance. An example of measuring during production is using an end-of-line body-in-white station to automatically check the vehicle’s structure before adding external components.
Accuracy and precision are taken very seriously – the overall safety of a vehicle, the product’s characteristics and economies of scale in production depend on it. Since the days of the Benz Patent-Motorwagen and the Ford Model T, vehicles have become increasingly complex, providing increased safety, longevity, performance and function. Production processes have become automated to offer more significant economies of scale.
To support these advancements, metrology has produced tools that measure with greater autonomy, accuracy, precision and speed. They offer benefits to producing human and machine-produced parts, aiding quality assurance and compliance with standards.
Metrological Tools
Various metrological tools exist to provide engineering and production-oriented measuring capabilities, each with its use cases and application trade-offs. Historically, metrology inspection was handled by a separate team and performed outside of the production flow (offline). Whilst numerous measurements are still conducted this way, automation is an essential goal for production. To meet this goal, inline metrology tools are progressing in their capabilities. The main goals of inline metrology tools are typically increased efficiency through less waste and lower costs with an overall increase in end-product quality.
Coordinate measuring machines (CMMs) are a great example of tools supplied to the automotive industry. They fit several use cases, two examples being:
- Quality Control – inspecting complex parts or systems for dimensional data to compare against specifications.
- Reverse Engineering
CMMs can measure complex objects with accuracy and precision. They also generate data that software can use to raise production flags and provide intelligence for early intervention in support of waste reduction and productivity. Today, CMMs are increasingly used in a near-inline and inline capacity, so quality assurance is taken directly to the production line and executed at much shorter intervals.
Aside from CMMs, other optical measuring systems such as vision inspection, laser and ultrasonic measurement systems offer inline measuring capabilities. Whilst each of these technologies has different use cases, they all support the automation of measuring in some form. Important inline capabilities include verifying dimensional accuracy, checking for defects, measuring forces and checking the integrity of parts.
Benefits of Metrology
By offering high-speed, accurate and precise measurements, the automotive industry can continue to support production capabilities to benefit shareholders and customers. With increasing inline capability, metrology can leverage techniques such as increased sampling rates, real-time reporting, the Internet of Things and machine learning to increase quality, lower costs, and increase profit. This will support the ability of the automotive industry to repeatedly produce high-quality vehicles time and time again.
Without Metrology, manufacturers would not have the capabilities to deliver vehicles with the quality, functionality and cost they currently have. More importantly, they would not have reached the levels of safety that we see today.
New designs, such as autonomous and electric vehicles and new production capabilities, such as robotics, will place different requirements on the industry. Metrology is well placed to meet these new requirements and continue its vital role.
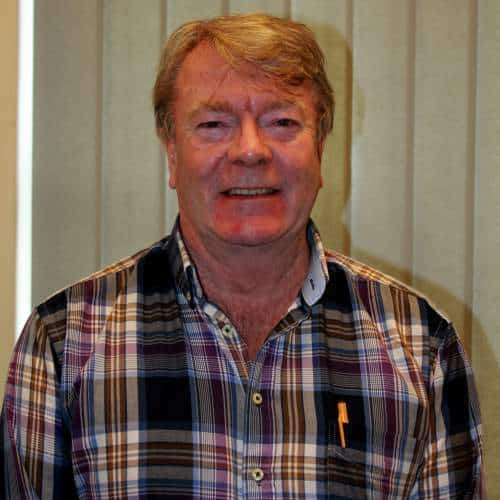
Jeff Eley is the founder and managing director of Eley Metrology, a leading company in the precision measurement industry. With decades of experience in metrology, Jeff has established himself as a respected figure in the field. Under his leadership, Eley Metrology has become renowned for its expertise in coordinate measuring machines (CMMs), digital height gauges, and granite metrology products. Jeff’s vision has driven the company to develop innovative solutions, including custom-designed CMMs and the flagship long-bore measurement machine (LBM). His commitment to excellence and customer-centric approach has positioned Eley Metrology as a trusted provider of high-precision measurement tools and services for industries such as aerospace, automotive, and manufacturing.