Sine plates and sine bars help designers and engineers measure angles, an essential job in any workshop. The most accurate tool for measuring incline and taper, sine plates and sine bars use precision engineering and simple trigonometry to verify quality and root out imperfections. Understanding their functions and uses helps designers and engineers strive for workpiece perfection.
What are the Differences Between Sine Plates and Sine Bars?
These related tools use many of the same parts and identical practices. However, they vary in key ways. Sine plates are broader than sine bars, and hinges attach them to a surface. This allows engineers and designers to fix larger workpieces for measurement or maintenance.
What Components Make Up a Sine Bar or Sine Plate?
Sine plates and sine bars use three main components. Firstly, they include the plate or bar itself, made from hardened, precision-engineered stainless steel. Although sine plates and sine bars rely on angularity and measure inclines, the steel itself is straight and flat.
Two cylinders with identical diameters allow the machine to pivot during measurement. Sine plates space these two cylinders at a regular distance to aid measurements. For imperial measurements, sine plates usually use 5 to 10 inches, while metric sine plates often a 200-millimetre spacing.
Thirdly, sine plates and sine bars use a height gauge or slip gauge blocks to lower and raise their angles to match workpieces. This allows the device to create right-angled triangles for comparing and measuring angled workpieces.
In addition, both sine plates and sine bars use base plates to level themselves and further height gauges to measure workpiece flatness. When using the correct equipment with high-quality manufacture and regular maintenance, sine plates and sine bars produce quality measurements to render products reliable and effective.
How Do Sine Plates and Sine Bars Work?
When it comes to sine plates and sine bars, it’s all about triangles. They implement trigonometric sine equations, hence their name. Both devices use such calculations to measure and validate workpiece angles.
Both devices aim to create a parallel between the workpiece base and the machine base. Using a sine equation, they calculate their elevation to mirror the workpiece’s desired angle. They then create this angle by inclining the plate or the bar to form a triangle’s hypotenuse. Inverting and resting a workpiece upon the plate or bar, therefore, creates a rectangle with parallel sides if the workpiece has the correct angle. If the workpiece’s angle fits specifications, it should form a flat surface when rested on the angled plate or bar. Through the plate or bar’s action, an engineer can measure the workpiece’s resulting flatness to assess its angle and conduct any necessary changes.
Due to a sine wave’s periodic oscillation, inaccuracies occur more frequently in steeper angles. Sine plates and bars can most accurately calculate angles between 15 and 45 degrees.
Like many of metrology’s simplest and most effective tools, sine plates and sine bars rely on simple equations and elegant components. Their accuracy and effectiveness make both plates and bars vital tools throughout engineering, from prototyping to quality control.
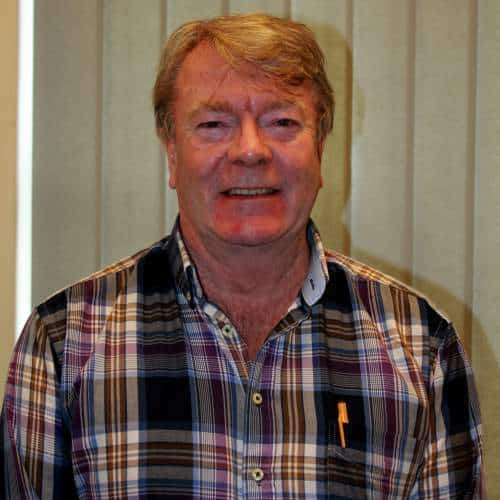
Jeff Eley is the founder and managing director of Eley Metrology, a leading company in the precision measurement industry. With decades of experience in metrology, Jeff has established himself as a respected figure in the field. Under his leadership, Eley Metrology has become renowned for its expertise in coordinate measuring machines (CMMs), digital height gauges, and granite metrology products. Jeff’s vision has driven the company to develop innovative solutions, including custom-designed CMMs and the flagship long-bore measurement machine (LBM). His commitment to excellence and customer-centric approach has positioned Eley Metrology as a trusted provider of high-precision measurement tools and services for industries such as aerospace, automotive, and manufacturing.