We specialise in manufacturing premium granite surface plates that provide an exceptionally flat reference surface for precise measurement and inspection requirements. Our surface plates are manufactured from superior-quality black granite, ensuring outstanding durability and resistance to wear.
They are non-responsive to temperature changes and offer an exceptionally sturdy measuring environment due to their thickness and weight.
All our surface plates conform to BS 817 (2008) and can be supplied with a UKAS Certificate of Calibration or an Eley Metrology Certificate of Calibration, ensuring immediate usability upon delivery.
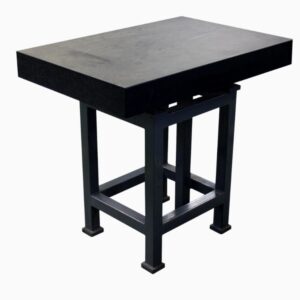
UK Manufactured
UKAS Certified Laboratory
Finest Quality Black Granite
Bespoke Sizes Available
Grades Supplied: 0, 1, 2
Get a Quote
Enter your requirements, and a member of our team will contact you shortly with your quote.
Bespoke Sizes Available
We can supply custom-sized granite surface plates to meet your precise specifications. Our team will be happy to help with any bespoke requirements you have.
Adjustable Support Stands
For our larger granite surface plates (900 x 600 x 100 and above), we supply robust steel support stands featuring three adjustable points to ensure optimal flatness regardless of surface.
View Our Complete Granite Surface Plate Range
Granite surface plates are a must for accurate measurement and provide a stable environment for inspection. They are non-responsive to temperature changes and offer an exceptionally sturdy measuring environment due to their thickness and weight.
You can now place an order with us directly at Eley Surface Plates, our new e-commerce store. Choose the size of your surface plate and select a certification option; your certified surface plate will then be despatched and ready for use upon arrival.
Grade 0
Grade 1
Grade 2
Granite Surface Plates FAQs
Granite is a type of igneous rock formed in the Earth millions of years ago. The composition of igneous rock contains many minerals, such as quartz which is extremely hard and wear-resistant. In addition to hardness and wear resistance, granite has approximately half the coefficient of expansion as cast iron. As its volumetric weight is approximately one-third that of cast iron, granite is easier to manoeuvre.
For machine bases and metrology components, black granite is the colour most used. Black granite has a higher percentage of quartz than other colours and is, therefore, the hardest wearing.
Granite is cost-effective, and cut surfaces can be exceptionally flat. Not only can it be hand-lapped to achieve extremes of accuracy, but re-conditioning can be performed without moving the plate or table off-site. It is entirely a hand-lapping operation and generally costs much less than re-conditioning a cast iron alternative.
These qualities make granite the ideal material for creating custom-size and custom-design machine bases and metrology components such as the granite surface plate.
Eley Metrology produces bespoke granite products that are created to support specific measurement requirements. These bespoke items vary from straight edges to tri squares. Due to the versatile nature of granite, the components can be produced in any size required; they are hard-wearing and long-lasting.
A granite surface plate is an essential investment for laboratories and test facilities. A granite surface plate of 600 x 600 mm can be mounted on a support stand. The stands provide a working height of 34” (0.86m) with five adjustable points for levelling.
For reliable and consistent measurement results, a granite surface plate is crucial. As the surface is a smooth and stable plane, it enables instruments to be carefully manipulated. They are also used in set-up of tooling, production and inspection.
The main advantages of granite surface plates are:
- Non-reflective
- Resistant to chemicals and corrosion
- Low coefficient of expansion compared with cart iron, so less affected by temperature changes
- Naturally rigid and hard-wearing
- The plane of the surface is unaffected if scratched
- Will not rust
- Non-magnetic
- Easy to clean and maintain
- Calibration and resurfacing can be done onsite
- Suitable for drilling for threaded support inserts
- High vibration damping
Due to being highly resistant to wear, granite surface plates are easy to maintain. With regular cleaning using a specialist granite cleaning fluid, the surface plates can remain reliable. We recommend that you use different areas of the granite surface to distribute the workload evenly.
Depending on the care and use of the surface plate, resurfacing will be required at some point. Granite surface plate calibration and resurfacing are vital to maintain original accuracy. Granite surface plates can be re-conditioned onsite with a quick turnaround to minimise disruption and downtime.
Eley Metrology can arrange an inspection of your granite equipment at regular intervals. Our team of highly skilled engineers can ensure that your granite equipment is maintained to optimum accuracy and quality levels.
Please get in touch if you would like a quote or more information on our granite surface plate inspection and maintenance packages.
Our granite surface plates are available in three grades: Grade 0, Grade 1 and Grade 2.
All our granite plates and tables are supported by a UKAS Certificate of Calibration and conform to BS 817 (2008).
Our larger surface plates (900 x 600 x 100 and up) are available with a high-quality steel support stand with three adjustable points to ensure flatness on any surface. Support stands can also be applied to the 600 and above size plates when you require a specific working height.
We can produce one-off or bespoke-sized granite surface plates to your specifications. Please contact our team to discuss your requirements.
Our team of engineers provide calibration and resurfacing for all sizes and grades of granite surface plates and tables. We can also calibrate granite parallels, master squares and master straight edges.
Our highly skilled team will hand-lap your granite back to the original specification in accordance with BS817 (2008) supported by a UKAS certificate of calibration.
Related Products and Services
• Granite Cleaning Fluid - The granite cleaning fluid solution developed by Eley metrology is a compound of special detergents and astringents. When applied to a granite surface, it will clean and remove all traces of oil, grease, cutting fluid and dirt
• Granite Surface Plates Calibration and Resurfacing - Our team of engineers provide calibration and resurfacing for all sizes and grades of granite surface tables and plates. We can also inspect granite parallels, master squares and master straight edges
• Surface Plate Support Stands - Our high-grade steel support stands can be produced alongside a granite plate to form a granite table
• Granite Surface Tables Accessories - In metrology, it is very common for customers to require threaded inserts to hold or clamp items in place during the measurement process
Find Out More
If you’d like more details about our range of granite surface plates, then our team are available to help.
Call Us: 01332 367475
Email: sales@eleymet.com
Send your enquiry via our contact form below;